隨著工業(yè)的發(fā)展,在工業(yè)生產(chǎn)過程中產(chǎn)生大量的工業(yè)廢水,其中來自造紙、醫(yī)藥、石化、油氣開采等行業(yè)這類工業(yè)廢水具有成分復雜、高COD、高含鹽量、有毒含量高和難降解的特點。此類難降解工業(yè)廢水若不經(jīng)過處理而直接排放,會污染地表水、地下水、土壤和耕地,影響植物及微生物的正常生長,從而影響人類的身體健康。目前難降解工業(yè)廢水已成為國內(nèi)外水處理領域的一大研究熱點及難題。
1 高級氧化技術研究現(xiàn)狀
高級氧化技術是在結合現(xiàn)代光、電、聲、磁、材料等相近學科的基礎上,對傳統(tǒng)水處理技術中的化學氧化方法進行改革而形成的一種新的技術方法。高級氧化方法主要包括Fenton 氧化法、電化學氧化法、光催化氧化法、濕式氧化法、超臨界水氧化法、臭氧催化氧化法等。
Fenton 氧化技術是利用H2O2在Fe2 + 的催化氧化作用下生成具有高反應活性的羥基自由基( ˙OH) ,˙OH 可以與大多有機物反應使其降解,F(xiàn)enton 試劑作為一種強氧化劑用于去除廢水中的有機污染物具有明顯的優(yōu)點,近年來Fenton 氧化技術在處理可生物降解有機物方面也取得了很大的進展。濕式氧化技術是從20 世紀50 年代發(fā)展起來的高級氧化技術,國內(nèi)對濕式氧化技術的研究相對較晚。該技術適用于濃度高、處理量小、有毒有害,并且采用生化法處理效果不顯著的難降解有機廢水的處理。
臭氧催化氧化是一種高級催化氧化技術,在催化劑的作用下,能夠加大水中臭氧溶解量,加強臭氧的氧化能力,進而提高氧化效率,對有機物有很好的去除效果。生物法是利用微生物降解代謝有機物為無機物來處理廢水。通過人為的創(chuàng)造適于微生物生存和繁殖的環(huán)境,使之大量繁殖,以提高其氧化分解有機物的效率。根據(jù)使用微生物的種類,可分為好氧法、厭氧法和生物酶法等。生物法可以作為臭氧催化氧化的后續(xù)工藝,但在實驗過程中與臭氧催化氧化部分同時進行。臭氧催化氧化- 生物法因其成本低,易實現(xiàn),效果好,在濃鹽廢水處理方面具有良好的發(fā)展前景。
2 高級氧化技術在難降解工業(yè)廢水處理中的應用
2. 1 高級氧化技術在制藥廢水處理中的應用
制藥廢水雖然產(chǎn)生量小,但是具有含鹽量高、污染物濃度高、污染嚴重、危害大等特點,采用常規(guī)的物化及生物法處理后難以達標,制藥廢水一直是水處理領域所關注的熱點和難點。郗金娥等經(jīng)過對某醫(yī)藥廢水的分析和研究,將廢水分為高鹽廢水、高濃度難生化廢水和綜合廢水。對高含鹽廢水采用二次蒸發(fā)系統(tǒng)回收一價鈉鹽,冷凝水進入調(diào)節(jié); 難生化廢水采用臭氧預處理,出水進入調(diào)節(jié)池。高鹽廢水及難生化廢水經(jīng)過處理后的出水與洗滌廢水、工程生活污水等充分混合,這種綜合廢水再采用兩級厭氧+ 好氧+ 高級氧化進行深度處理。
運行結果表明,BOD、COD 的去除率分別達到99. 5%、99. 8%,出水水質(zhì)穩(wěn)定,并且滿足污水綜合排放標準( GB8978 - 1996) 及山東省小清河流域水污染物綜合排放標準( DB37 /656 - 2006) 中對一般保護區(qū)域最高允許排放濃度標準要求。工藝改進后,與現(xiàn)有工況比較,COD 總削減量11. 02t /a,削減率可達50%以上,處理效果有了明顯的提升。按照處理量500m3 /d 計算,廢水的直接處理成本為10. 06 元/ m3。

吳菊珍等針對某農(nóng)藥廢水的特點,在不改變原處理工藝,同時又不增加處理成本的條件下,對原處理工藝進行技術改造。采用鐵炭微電解+ Fenton高級氧化聯(lián)合處理工藝對此農(nóng)藥廢水進行了預處理,去除COD、Cl -、重金屬等有毒物質(zhì),再采用厭氧+ 好氧生物法進行深度處理,出水達到污水綜合排放標準( GB8978 - 1996) 一級排放要求。
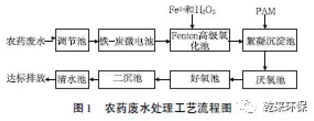
張紅艷采用濕式氧化技術對某農(nóng)藥廠的高鹽度、難降解的農(nóng)藥廢水處理工藝進行了改進,研究結果表明,當反應溫度280℃、氧分壓4. 2MPa、反應液初始pH 值2. 0、反應時間2. 5h,廢水中的COD 去除率高達98%、色度去除率高達99%。與原工藝比較,COD 去除率提高了23%,處理效果有了明顯的提高。濕式氧化處理技術具有很好的COD 去除效果,同時具有顯著的脫色作用,而且不會造成二次污染,適用于農(nóng)藥廢水的處理。
2. 2 高級氧化技術在石化廢水處理中的應用
石化工業(yè)廢水具有污染物含量變化大、毒性大、成份非常復雜等特點。因此對不同種類的石化廢水往往需要綜合幾種不同的處理技術對其進行處理才能達到理想的處理效果。目前國內(nèi)石化工業(yè)廢水處理設施大多難以滿足當前環(huán)保排放標準的要求,急需對處理工藝進行升級改造。
易斌采用活性炭吸附+ Fenton 氧化工藝對某化工生產(chǎn)車間的高鹽有機廢水進行處理,研究結果表明,單獨采用活性炭吸附后,廢水COD 的去除率最大為47. 5%,經(jīng)過活性吸附+ Fenton 氧化工藝聯(lián)合處理后,廢水COD由13 650 mg /L 降低至560mg /L,去除率達到95. 9%。
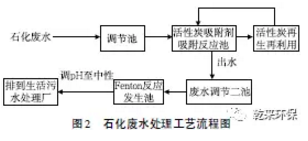
采用此工藝再生活性炭可以將其吸附性能再生至原有水平,活性炭再生率可達100. 5%,再生費用約為1800元/噸,比新購置活性炭的價格低很多,同時可以降低此類有機廢水的處理費用,因此采用活性炭吸附+ Fenton氧化工藝可以用于此類高鹽有機廢水的處理。
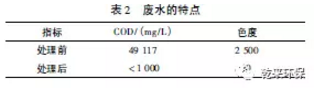
龔小芝等采用缺氧+ 好氧+ 催化臭氧氧化工藝處理某石化廠的含鹽廢水,在進水COD 為200 ~350mg /L 的條件下,經(jīng)過生化處理后的出水COD 穩(wěn)定在50 ~ 60mg /L,COD 去除率穩(wěn)定在75%。在生化出水為54mg /L 的條件下,經(jīng)過連續(xù)催化臭氧氧化處理后,出水COD 穩(wěn)定在20mg /L 以下,COD 去除率大于70%
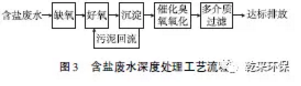
2. 3 高級氧化技術在油氣開采廢水處理中的應用
油氣開采廢水主要由油氣井采出水和鉆井廢水組成,油氣井采出水是伴隨石油、天然氣被采出的廢水,鉆井廢水是在油氣井鉆探開采過程中所產(chǎn)生的污水。油氣廢水是一種高含鹽含油的特殊廢水,該類廢水含有大量的油類、礦物質(zhì)、氯離子,重金屬、高分子有機化學物等,因此難以處理。旺迎春采用酸析+ Fenton 氧化+ 活性炭吸附組合工藝處理川西某氣井采氣廢水,研究結果表明,在最佳實驗條件下( pH = 1、H2O2 /COD = 7、n( H2O2 /Fe2 + ) = 3、反應時間= 2h) ,COD、SS、油類物質(zhì)、色度的去除率分別為81%、99%、95%、99%,酸析+ Fenton 氧化+ 活性炭吸附組合工藝對采氣廢水的處理效果顯著,處理后出水澄清。綜合考慮處理效果和經(jīng)濟性,將芬頓試劑、吸附材料分批次添加以提高反應效率,COD 去除效果顯著提高,在最佳工藝條件下,處理后的COD 小于100mg /L,達到《污水綜合排放標準》一級標準。經(jīng)測算,采用此工藝處理此廢水運行成本為19. 64 ~34. 88 元/噸。
楊偉等采用Fenton 高級氧化和活性炭吸附法處理高含鹽難降解的采油廢水,研究結果表明,廢水pH 為3,F(xiàn)enton 試劑c( H2O2) / c( COD) = 2,n( H2O2) / n( Fe) = 10,氧化時間為40min 時,F(xiàn)enton高級氧化對廢水中的COD、油的去除效果最佳。氧化對活性炭吸附具有促進作用,吸附時間為45min,COD 去除率為75%,出水COD為48mg /L,滿足遼寧省污水綜合排放標準( DB21 /1627 - 2008) 要求。重烷基苯磺酸鹽是三元復合驅(qū)技術的主表面活性劑,是油田三次采油的核心助劑。十二烷基磺酸鈉( SDS) 廢水具有COD 高、pH 值高和鹽度高的特點,采用常規(guī)的物化或生物處理法,處理成本高、處理效果不理想,出水水質(zhì)不能達到排放標準。郭超采用UV/Fenton 與生物接觸氧化聯(lián)合工藝處理十二烷基磺酸鈉( SDS) 混合廢水,處理后水質(zhì)滿足《城市污水處理廠污染物排放標準》( GB18918 - 2002) 一級B 標準。經(jīng)過工程測算,采用此工藝處理SDS 綜合廢水,綜合成本為16. 59 元/噸,與第三方處理方式比較,處理成本有明顯的降低。此項研究成果為SDS 廢水處理的無害化、資源化處理積累了基礎數(shù)據(jù)。
3 結論與展望
高級氧化技術具有氧化能力強、氧化過程無選擇性等特點,在難降解工業(yè)廢水處理中的具有良好的應用前景,但還需要通過優(yōu)化組合高級氧化技術,不斷提高各種高級氧化技術系統(tǒng)的效率并降低成本,另外將高級氧化技術與傳統(tǒng)的生化處理技術聯(lián)合運用,以達到處理效果與經(jīng)濟成本的最優(yōu)化將是未來難處理工業(yè)廢水處理的研究方向。
來源:《環(huán)保科技》 作者:李鳳娟等
特此聲明:
1. 本網(wǎng)轉載并注明自其他來源的作品,目的在于傳遞更多信息,并不代表本網(wǎng)贊同其觀點。
2. 請文章來源方確保投稿文章內(nèi)容及其附屬圖片無版權爭議問題,如發(fā)生涉及內(nèi)容、版權等問題,文章來源方自負相關法律責任。
3. 如涉及作品內(nèi)容、版權等問題,請在作品發(fā)表之日內(nèi)起一周內(nèi)與本網(wǎng)聯(lián)系,否則視為放棄相關權益。