燒結(jié)煙氣是鋼鐵企業(yè)大氣污染物排放的主要來(lái)源,主要包含二氧化硫、氮氧化物、顆粒物、二英、重金屬(鉛、砷、鎘、鉻、汞等)、氟化物和揮發(fā)性有機(jī)物(VOCs)等多種污染物,其中前五種污染物對(duì)環(huán)境的影響最為突出,尤其是二氧化硫和氮氧化物,二者是霧霾主要成分PM2.5形成的重要前體物?!朵撹F燒結(jié)、球團(tuán)工業(yè)大氣污染物排放標(biāo)準(zhǔn)》(GB28662-2012)等一系列鋼鐵行業(yè)新排放標(biāo)準(zhǔn)從2012年10月1日正式實(shí)施,并于2015年1月1日起實(shí)行最新的排放標(biāo)準(zhǔn)。
與此前標(biāo)準(zhǔn)相比,污染物排放濃度限值均大幅收嚴(yán),同時(shí)新增了二惡多污染物協(xié)同控制英等污染物的排放限值。據(jù)《中國(guó)鋼鐵工業(yè)環(huán)境保護(hù)統(tǒng)計(jì)2014》會(huì)員單位上報(bào)信息數(shù)據(jù)統(tǒng)計(jì),二氧化硫、氮氧化物和煙粉塵排放量分別為663005.89t、578269.12t和509687.19t,導(dǎo)致燒結(jié)生產(chǎn)中二惡英生成量增加。因此,在新的環(huán)保要求下,燒結(jié)煙氣污染物的控制已經(jīng)不再是簡(jiǎn)單的除塵脫硫,而是需要在單一污染物的治理基礎(chǔ)上,考慮多污染物的協(xié)同控制,從而實(shí)現(xiàn)所有污染因子達(dá)標(biāo)排放。那么,開(kāi)發(fā)新型高效的污染物凈化脫除技術(shù)就成為現(xiàn)階段亟需解決的問(wèn)題。
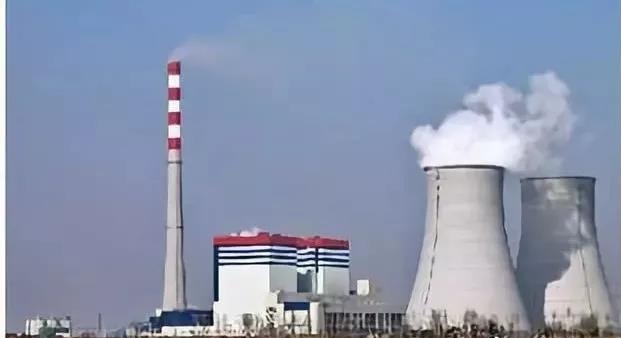
一、鋼鐵行業(yè)燒結(jié)煙氣多污染物排放特征
1.二氧化硫
燒結(jié)煙氣中的二氧化硫主要來(lái)源于鐵礦石和煤粉等固體燃料,其中的硫化物與有機(jī)硫被氧化為二氧化硫釋放,產(chǎn)生量為0.8~2kg/t,排放濃度一般在300~10000mg/m3。
因鐵礦石和原煤品位差異,國(guó)內(nèi)鋼企燒結(jié)煙氣中二氧化硫的排放濃度為200~6000mg/m3,因此在選擇脫硫工藝時(shí)要做到因地制宜。
2.氮氧化物
燒結(jié)過(guò)程中產(chǎn)生的氮氧化物80%~90%來(lái)源于燃料中的氮,且90%以上為一氧化氮,5%~10%為二氧化氮以及微量一氧化二氮,產(chǎn)生量為0.4~0.7kg/t,排放濃度一般為200~350mg/m3。燃料品質(zhì)差異導(dǎo)致燒結(jié)煙氣中氮氧化物排放濃度介于100~600mg/m3之間,個(gè)別無(wú)法滿(mǎn)足排放限值的企業(yè)面臨增加脫硝裝置來(lái)實(shí)現(xiàn)達(dá)標(biāo)排放的問(wèn)題。
3.粉塵
燒結(jié)生產(chǎn)粉塵來(lái)源于燒結(jié)原燃料,燃燒使抽風(fēng)煙道排出大量的含塵廢氣。該工序粉塵產(chǎn)生量為20~40kg/t(以燒結(jié)礦計(jì)),排放濃度一般為1000~5000mg/m3,成分較復(fù)雜,主要包括鐵的氧化物、堿金屬、二氧化硅、二氧化鈦和二噁英等。目前,經(jīng)過(guò)脫硫后布袋除塵器或濕式電除塵器的粉塵排放濃度均在40mg/m3以下,滿(mǎn)足排放要求。
4.二噁英
燒結(jié)工序中的二噁英主要來(lái)自于燒結(jié)料層中,焦粉、煤等含碳成分和含鐵原料中的含氯載體,以銅、鐵催化在氧化氣氛中于250℃~450℃條件下,在干燥預(yù)熱帶形成二噁英。此過(guò)程中,二噁英同類(lèi)物以多氯代二苯并呋喃(Polychlorinateddibenzofurans,PCDFs)為主,大部分燒結(jié)機(jī)二噁英排放濃度均≤1ng-TEQ/m3,但也存在處于1~5ng-TEQ/m3范圍內(nèi)的燒結(jié)機(jī),若想滿(mǎn)足0.5ng-TEQ/m3排放限值,也需在未來(lái)調(diào)配原料品位或增設(shè)相應(yīng)二噁英處理設(shè)施予以應(yīng)對(duì)。
二、燒結(jié)煙氣多污染物協(xié)同控制技術(shù)
截至“十二五”末,絕大部分鋼企燒結(jié)機(jī)都安裝了燒結(jié)煙氣脫硫裝置,但氮氧化物、汞和二英的治理工作則剛剛起步,鮮有工程化案例。就燒結(jié)煙氣脫硫而言,目前主要采用石灰(石)-石膏法、循環(huán)流化床法等成熟脫硫技術(shù);對(duì)于燒結(jié)煙氣脫硝,目前還沒(méi)有匹配的控制技術(shù),參照火電、水泥等行業(yè)煙氣氮氧化物控制經(jīng)驗(yàn),一般采用選擇性催化還原法(SCR)、選擇性非催化還原法(SNCR)等脫硝技術(shù),但燒結(jié)煙氣溫度較低,通常在180℃以下,難以達(dá)到傳統(tǒng)脫硝催化劑反應(yīng)的溫度,依靠GGH換熱無(wú)疑大大增加了系統(tǒng)能耗,且冶金行業(yè)不同于電力行業(yè),未有脫硫或脫硝電價(jià)補(bǔ)貼,因此大大增加了運(yùn)行成本。
1.半干法(濕法)脫硫除塵+活性炭+SCR(低溫SCR)協(xié)同凈化
半干法(濕法)脫硫+SCR脫硝工藝成功應(yīng)用于電力行業(yè),脫硫效率≥95%,脫硝效率為70%~85%。該組合工藝技術(shù)成熟,污染物脫除效率高,適用性強(qiáng),可滿(mǎn)足最新的排放標(biāo)準(zhǔn),尤其適用于目前我國(guó)已建成燒結(jié)脫硫的實(shí)際情況,業(yè)主只需增設(shè)脫硝部分即可實(shí)現(xiàn)聯(lián)合脫除,無(wú)需推倒重來(lái)。但主要問(wèn)題是,目前商業(yè)催化劑催化活性溫度窗口為280℃~400℃,而半干法脫硫出口溫度為100℃~140℃,濕法脫硫出口溫度更低,因此若想移植此工藝至燒結(jié)脫硝應(yīng)用,將煙氣加熱至催化劑活性溫度窗口,勢(shì)必會(huì)大大增加能耗,且復(fù)雜的燒結(jié)煙氣成分對(duì)催化劑的使用壽命和維護(hù)成本都會(huì)構(gòu)成較大影響。而目前仍處于實(shí)驗(yàn)室或中試規(guī)模的Mn基、Cu基等低溫SCR脫硝催化劑的抗中毒性能還有待檢驗(yàn)?;钚蕴客ㄟ^(guò)吸附Hg0來(lái)實(shí)現(xiàn)對(duì)汞的脫除,但吸附效率相對(duì)較低。二噁英在高效除塵過(guò)程中可實(shí)現(xiàn)部分脫除,并通過(guò)后續(xù)的吸附或者催化分解可進(jìn)一步去除。目前,由浙大能源工程學(xué)院研制的CDS-FGD+SCR協(xié)同技術(shù)已通過(guò)中試試驗(yàn),獲得了良好效果。
2.活性焦(炭)移動(dòng)床協(xié)同凈化
活性焦(炭)協(xié)同凈化以物理-化學(xué)吸附和催化反應(yīng)原理為基礎(chǔ),能實(shí)現(xiàn)一體化脫硫、脫硝、脫二噁英、脫重金屬及除塵的煙氣集成深度凈化,解析二氧化硫制硫酸,而氮氧化物則在還原劑氨的氣氛下,經(jīng)由催化作用生成了無(wú)害的氮?dú)夂退?,整個(gè)反應(yīng)過(guò)程無(wú)廢水、廢渣排放,無(wú)二次污染,是適應(yīng)燒結(jié)煙氣脫硫和集成凈化的先進(jìn)環(huán)保技術(shù)。從日本住友在太鋼450m2燒結(jié)機(jī)上興建的國(guó)內(nèi)首套全進(jìn)口活性焦協(xié)同凈化項(xiàng)目,到由上??肆颉⒅幸北狈接诮K永鋼2號(hào)450m2燒結(jié)機(jī)建成的首套自主知識(shí)產(chǎn)權(quán)的活性焦一體化脫除技術(shù),表明我國(guó)已在此領(lǐng)域有了較大突破,投資和運(yùn)行成本均有較大幅度的降低,理論上可實(shí)現(xiàn)90%以上的脫硫效率與50%以上的脫硝效率,雖然仍存在較多實(shí)際問(wèn)題,如運(yùn)行穩(wěn)定性,但此法作為目前唯一在國(guó)內(nèi)具備成功應(yīng)用案例的協(xié)同治理工藝,隨著進(jìn)一步的摸索改進(jìn),可作為一種較適用的治理技術(shù)。
3.新型一塔式固定床干法聯(lián)合凈化
此工藝由北京科技大學(xué)環(huán)境工程系大氣污染防治梯隊(duì)研發(fā),依靠層進(jìn)式的脫硫—脫硝—脫汞—脫二英一塔式凈化技術(shù)路線(xiàn)。首先,經(jīng)除塵后的燒結(jié)煙氣通過(guò)高硫容的活性焦實(shí)現(xiàn)對(duì)二氧化硫的高效脫除;隨后,利用雙功能強(qiáng)氧化催化劑,實(shí)現(xiàn)進(jìn)一步的脫汞、脫二噁英;
最后,采用高效低溫SCR催化劑,實(shí)現(xiàn)對(duì)氮氧化物的低溫脫除。目前,該工藝已完成實(shí)驗(yàn)室測(cè)試,在≤150℃的條件下取得了脫硫、脫二英效率≥90%,脫硝、脫汞效率≥70%的優(yōu)良活性。高硫容活性焦可減少其再生頻率,提升其機(jī)械性能,減少損耗;雙功能催化氧化材料(不使用鹵素氧化劑),促使一氧化氮被部分被氧化為二氧化氮,為下一步低溫SCR脫硝創(chuàng)造有利條件。該工藝尚需進(jìn)行工程實(shí)踐測(cè)試,以此來(lái)檢驗(yàn)其對(duì)實(shí)際燒結(jié)煙氣復(fù)雜成分的抗性,結(jié)合實(shí)驗(yàn)數(shù)據(jù)進(jìn)一步探討應(yīng)用此項(xiàng)技術(shù)實(shí)現(xiàn)燒結(jié)煙氣協(xié)同治理的可能性。
4.臭氧氧化+催化液相吸收凈化
該工藝主要是先將煙氣中的一氧化氮通過(guò)臭氧的強(qiáng)氧化作用轉(zhuǎn)變?yōu)槎趸?,同時(shí)部分Hg0也會(huì)轉(zhuǎn)變?yōu)镠g2+,再將煙氣引入濕式洗滌塔中參與反應(yīng),脫除二氧化硫和二氧化氮等酸性氣體污染物的同時(shí),在雙效催化劑的作用下,煙氣中含有的剩余Hg0也會(huì)轉(zhuǎn)變?yōu)镠g2+,二噁英也將分解生成二氧化碳從而一并經(jīng)由液相吸收,實(shí)現(xiàn)協(xié)同凈化,理論上可獲得脫硫效率≥95%、脫硝效率≥80%的較優(yōu)參數(shù)。此工藝原理看似簡(jiǎn)單,但對(duì)于強(qiáng)氧化劑臭氧添加量尚不能做到精確控制,量少會(huì)導(dǎo)致整個(gè)反應(yīng)脫除效率下降,過(guò)多則會(huì)帶來(lái)臭氧逃逸的嚴(yán)重二次污染,因此雖然本方法可以通過(guò)對(duì)現(xiàn)有的濕法脫硫進(jìn)行改造予以實(shí)現(xiàn),但是對(duì)諸如臭氧逃逸、固體廢棄物處置等現(xiàn)實(shí)問(wèn)題的影響,仍需進(jìn)一步論證解決。
來(lái)源:冶金經(jīng)濟(jì)與管理
特此聲明:
1. 本網(wǎng)轉(zhuǎn)載并注明自其他來(lái)源的作品,目的在于傳遞更多信息,并不代表本網(wǎng)贊同其觀(guān)點(diǎn)。
2. 請(qǐng)文章來(lái)源方確保投稿文章內(nèi)容及其附屬圖片無(wú)版權(quán)爭(zhēng)議問(wèn)題,如發(fā)生涉及內(nèi)容、版權(quán)等問(wèn)題,文章來(lái)源方自負(fù)相關(guān)法律責(zé)任。
3. 如涉及作品內(nèi)容、版權(quán)等問(wèn)題,請(qǐng)?jiān)谧髌钒l(fā)表之日內(nèi)起一周內(nèi)與本網(wǎng)聯(lián)系,否則視為放棄相關(guān)權(quán)益。